views
What Causes Glass to Crack in Welding?
When welding, the heat of the arc can cause glass to crack. The most common cause of this is when the weld pool is too small. When the weld pool is too small, the heat of the arc causes sudden thermal expansion and contraction of the metal. This can cause cracks in the glass. Other causes of glass cracking include improper technique, using brittle glass, and using a poorly made welder. To prevent glass from cracking during welding, pay attention to these tips:
Use a large enough weld pool and make sure that you have enough material to hold on to when welding. A large weld pool will reduce the amount of stress on the glass and minimize the chance of it cracking.
Use a consistent technique; keep your fingers away from the glass and maintain consistent pressure throughout the weld. If you are using a stick welder, make sure that you use an automatic feed system so that you do not have to apply constant pressure to the wire.
Use quality glass; choose tempered or heat-treated glass that has been designed for welding. Bending or breaking this type of glass can lead to cracks.
Fixing a Broken Glass Weld Cap
If you are experiencing a broken glass weld cap, there are a few things that you can do to fix the situation. First, try to reach the glass with a tool such as a butter knife. If this is not possible, you will need to use a special tool called a glass cutter. Once you have reached the glass, you will need to use the glass cutter to slice off the broken pieces of the weld cap. Finally, you will need to clean the area and re-attach the weld cap.
Welding Glass Crack Prevention Tips
If you're welding with a glass-shielded electrode, there's a good chance you'll get glass crack. Here are some tips for preventing it:
1. Select an appropriate filler metal. If your welding rod is made of TIG (tungsten inert gas) or MIG (manganese inert gas) electrodes, stick with those. They're less likely to produce glass cracks.
2. Select your welding tip with care. If your weld rod is made from a low-alloy steel, then choose a welding tip made from the same material. A low-alloy content weld rod will crack more easily than a higher-alloy weld rod will.
3. Don't overheat the joint. When you overheat the joint, the metal becomes too soft and it's easier to break the bonds between the atoms in the metal and form cracks. Welding temperatures should not exceed 550 degrees Fahrenheit (285 degrees Celsius).
4. When possible, use an electric arc welder. An electric arc welder uses a continuous flow of electricity to heat up the weld zone until it reaches its melting point, at which point the two metals will join together. This type of welder is less likely to produce sparks.
Conclusion
If you are having trouble fixing the glass inside the welding cap, there are a few things that you can do to try and remedy the situation. First, make sure that you have everything that you need in order to fix the glass inside the welding cap. This could include a welder’s torch, flux, wire, and solder. Next, heat up the soldering iron until it is hot enough to melt the solder. Then, attach one end of the wire to one side of the glass and attach the other end of the wire to another part of the glass so that it forms a loop. Finally, place solder on top of this loop and hold it down until it has melted.
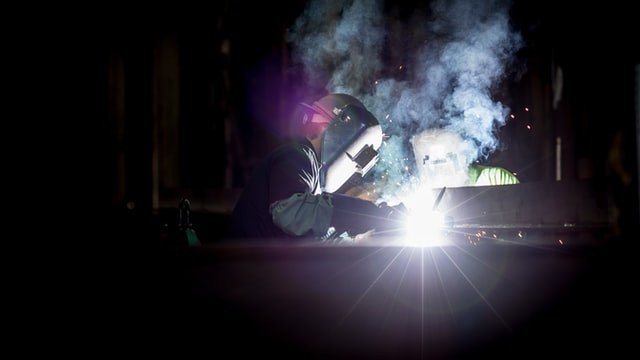
Facebook Conversations